ロケーション管理とは?3つの管理方法やメリット・注意点を紹介
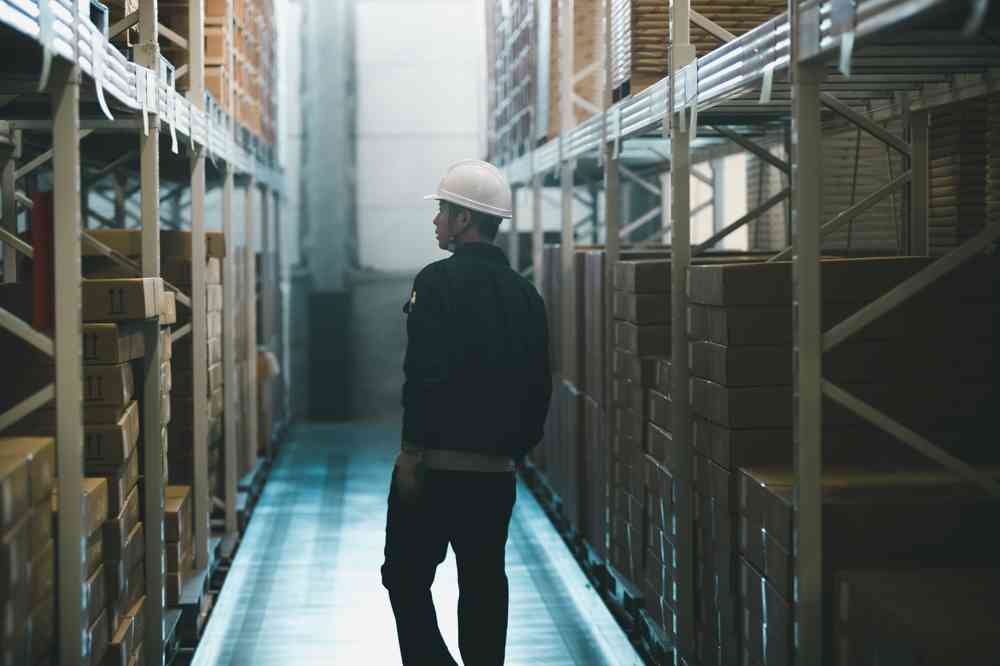
倉庫業務において商品の保管場所を番地化する管理方法「ロケーション管理」。導入することで倉庫作業の効率化・精度向上などが期待できます。本記事では、ロケーション管理とは何か?をはじめ、代表的な3つの管理方法、導入のメリット、実施する際のポイント等を解説します。
目次
ロケーション管理とは?
倉庫業務における「ロケーション管理」とは、商品の保管場所を番号化して整理することで、効率的な管理を実現するための手法です。
倉庫や保管スペースに住所のような番号を与えることで、どこに何が置かれているのか?を一目で把握できるようにするための措置でありつつ、作業の効率化やミスの削減をサポートしてくれる仕組みです。
大量の商品を扱う企業にとっては、倉庫業務の基盤ともいえる重要なシステムと言えます。
平置き
平置きとは、棚を使わず床に直接商品を置く保管方法です。ただし、一般的には床よりもパレットなどの荷役台に在庫を置くケースが多いようです。
平置きの強みは、大きな機材や不規則な形状の商品でも柔軟に保管できるうえ、設置コストが低い点です。一方で、保管物が増えると整理が難しくなるため、効率的な管理には工夫が求められます。
例えば、ロケーション管理によって保管エリアを番号や区画で分けることで、探す時間を短縮するなどの対処が多くの現場で採用されています。
ラック
ラック(置き)とは、商品を棚に収納して管理する方法です。ラックを使えば、平置きよりもスペースを多く使うことができるため、保存効率や作業効率が格段に上がります。
棚ごとに番号を振ることで、必要な物をすぐに取り出せる仕組みを整えられるため、倉庫や工場などで広く採用されている方式です。
ロケーション管理の3つの管理方法
ロケーション管理には、3つの代表的な管理方法があります。それぞれの特徴を、以下に解説します。
固定ロケーション
固定ロケーションは、商品の保管場所をあらかじめ固定する管理方法です。
「商品Aは棚Bの下段にある」といった要領で、特定の商品が常に同じ場所にあるため、発見するコストが低く抑えられる点がメリットであり、売れ筋商品の管理に適しています。
その反面、保管スペースに空白が生まれやすいため、種類が多い商品や激しく在庫数が変動する商品には不向きと言えます。
フリーロケーション
フリーロケーションは、商品の保管場所に法則を与えず、その都度空いているスペースに保管していく方法です。
この管理方法のメリットは、スペースを無駄なく活用でき、在庫の種類や量が大きく変動する状況にも、柔軟に対応できる点です。一方で、どこに何が保管されているか?を把握するためには、環境ごとのルール整備が必要となるでしょう。
ダブルトランザクション
ダブルトランザクションとは、在庫の保管だけを行うストックエリアと、出荷作業を行うだけのピッキングエリアを完全に分ける手法です。
つまり、普段の出荷作業ではピッキングエリアのみを人が往来することで、作業スピードを上げつつ保管エリアの導線管理を省くことができます。ただし、ピッキングエリアの商品が減ったタイミングで、一度に大量の商品をストックエリアからピッキングエリアに運ぶ必要があります。
この方法のメリットは、ピッキング作業が効率化され在庫の正確性も向上する点です。しかし、エリアを分けるためのスペースと運用ルールが必要となるため、適切な計画と運用スキルが前提となる管理手法と言えるでしょう。
ロケーション管理を導入するメリットとは?
ロケーション管理を適切に導入すれば、大きなメリットを期待できるでしょう。具体的なメリットの内訳について、以下に解説します。
倉庫作業の効率化・迅速化を実現できる
適切なロケーション管理は、効率的かつ素早い倉庫作業を実現してくれます。
例えば、固定ロケーションを採用すれば商品を探す時間を大幅に短縮でき、フリーロケーションならばスペースを有効活用しながら柔軟な管理が実践できるでしょう。
また、ダブルトランザクションでは頻繁に出荷される商品をピッキングエリアに集約することで、両者の短所を補い合う運用が可能となります。状況に合わせてこれらの手法を組み合わせることで、より効率的な倉庫運営が可能になるはずです。
倉庫作業の精度・サービスの質向上を実現できる
ロケーション管理を導入することで、在庫の配置や管理が適正化され、出荷ミスの防止や在庫切れのリスクを低減できます。
出荷作業の精度が上がれば、誤発送や商品の損傷などのミスも減少するため、顧客からの評価を高める効果も期待できるでしょう。正確でスムーズな業務は企業の信頼性を長期的に高め、リピーターの獲得にも役立つでしょう。
倉庫管理費用を最適化できる
ロケーション管理を活用すれば、無駄なコストを多角的に削減できます。適切なロケーション管理はピッキングの作業効率をアップさせ、人件費の削減を実現してくれます。
また、フリーロケーションで倉庫の保管効率をアップさせれば、多少入荷の商品数が増えたとしても、大きな倉庫への移転をする必要もなくなるため、倉庫費用の削減にも寄与するはずです。
ロケーション管理の課題・注意点
ロケーション管理の導入には、一定の注意点が存在します。具体的なポイントについて、以下に詳しく解説します。
保管場所が近い商品を間違えてピッキングしてしまう
ロケーション管理の品質によっては、保管場所が近い商品や名前が似ている商品を、間違えてピッキングしてしまうリスクがあります。
この課題を防ぐためには「名前が見た目が似ている商品を隠して保管する」といった工夫や、ラベルを分かりやすく表示するなどの対処が重要となります。
また、バーコードやシステムによるチェックを併用することでも、このようなヒューマンエラーを減らすことができるでしょう。
新しい保管スペースの確保が難しい
ロケーション管理では、商品を「間口」というスペース単位で管理する方式が一般的ですが、商品数が増えてくると新たな間口を確保することが難しくなります。
多くの場合では、特定の不良在庫がスペースを圧迫した結果であるため、流動性の低い不良在庫については、個別に間口を設けず1ヶ所にまとめてしまうことをおすすめします。
この方法をとれば、ロケーション管理による効率性を邪魔することなく、不良在庫による弊害を緩和することが可能です。
不良在庫が多く保管効率が下がる
出荷頻度が低い不良在庫が増えると、限られた保管スペースが占有され、保管効率が低下してしまいます。
ロケーション管理の工夫で不良在庫の悪影響をある程度は抑えることができますが、根本的にこの課題を解決するためには、定期的な在庫の見直しや、不良在庫の適切な処分が必要不可欠です。
また、商品の回転率をよく把握し、優先度のある保管計画を立てることでも、効率的な運用が可能となるでしょう。
ロケーションを変更する度に作業効率が下がる
ロケーションを変更して間もない時期には、作業員が新しい配置に慣れるまで効率が低下することがあります。
とりわけ、変更後のロケーションが十分に周知されていない場合や、大がかりな変更が実施されたケースでは、一時的に出荷スピードに影響が出ることが予測されます。
この課題に対処するためには、変更後のロケーションを分かりやすく表示したり、スタッフへの周知やトレーニングを徹底することが重要となるでしょう。
ロケーション管理の課題を改善する方法
ロケーション管理で生じる課題を克服する具体的な改善方法について、以下に詳しく紹介します。
自社の商品と倉庫にあった管理方法を選ぶ
ロケーション管理を成功させるには、自社の商品特性や倉庫環境に適した手法を選ぶことが、何よりも重要です。
例えば、種類が少なく大量に出荷される商品が多いケースでは固定ロケーションが適しています。一方で、商品数が多く出荷数の変動も激しい場合には、フリーロケーションやダブルトランザクションが効果的となります。
また、倉庫の広さや設備の機能なども考慮に入れたうえで、適切な方法を選ぶことも重要です。もし最適な手法がわからなければ、同業他社の運用方法を参考にするのも良いでしょう。
出荷頻度が高い商品は取り出しやすい場所に保管する
出荷頻度に合わせた保管場所の配置こそが、作業効率を向上させるポイントです。
例えば、最も出荷頻度の高い商品群を倉庫内の入口付近や通路に近い場所に配置することで、ピッキング作業の時間を大きく短縮できるはずです。
また、作業導線を意識したレイアウトを工夫すれば、無駄な移動を減らして全体の流れを効率化できます。倉庫内の導線をヒートマップなどに見える化すれば、こうした情報を客観的に分析できるようになるでしょう。
ミス防止のため似た商品は離れた場所に保管する
ピッキングミスを防ぐためには、見た目や名前が似ている商品を、原則として離れた場所に保管することが有効です。
例えば、似た形状や色の商品を隣り合わせにしてしまうと、不慣れな従業員が間違えて取り出してしまうリスクが高まります。逆に言えば、これらの商品に物理的な距離を与えてしまえば、こうしたミスをほぼゼロにすることができます。
また、保管場所に目立つ注意書きをつけることでも、ミスの発生率を抑制できるはずです。
棚の大きさ・番号の割り振りを工夫する
商品のサイズや分量に合った棚を選びつつ、わかりやすい識別番号を割り振ることも、スムーズな作業環境を整える鍵となります。
例えば、大型商品には広いスペースを確保できる棚を、小さな商品には細かく区分けされた棚を用意することで、保管効率や移動コストが大きく最適化されます。
また、番号の割り振りを整理して、棚ごとの位置が一目で把握できるようにすれば、ピッキングや在庫確認の時間を短縮できるはずです。こうした細かい工夫こそが、倉庫全体の管理の効率化や作業ミスの減少をサポートしてくれます。
不良在庫はまとめて保管する
限られた保管スペースを有効に活用するためには、不良在庫はまとめて一箇所に保管することも一手です。
流動性の低い商品がバラバラに配置されているとスペースに無駄が生じ、作業効率も低下します。しかし、こうした不良在庫は一箇所にまとめることで、不要な移動を減らし他の商品を効率的に配置できるようになるでしょう。
また、不良在庫の処分や在庫整理もスムーズに実施できるようになれば、倉庫全体の管理をよりシンプルにする、という副次効果も期待できます。
WMS(倉庫管理システム)を導入する
WMS(倉庫管理システム)とは、在庫管理やピッキング作業を効率化するシステムです。
このシステムを導入すると、商品の入出庫や在庫状況をリアルタイムで把握できるようになります。さらに、バーコードやハンディターミナルを活用すれば、ピッキングや検品の正確性が大きく向上し、作業時間の短縮にも寄与してくれます。
倉庫作業が一定規模を超えた段階にて、導入を検討すると良いでしょう。
▷倉庫管理システム(WMS)19選比較|機能や価格・小規模・クラウド向けのシステムを紹介
倉庫管理を専門業者に依頼する
倉庫管理を専門業者に依頼することでも、業務の効率化やコスト削減が期待できます。
専門業者は高度なノウハウやシステムを持ち、在庫管理やピッキング作業を正確かつスピーディーに行えます。また、自社は本来の業務に集中できるようになります。
自社で全てを管理するのが難しい場合や、コア業務に集中したい企業にとっては、常に有効な選択肢の一つと言えるでしょう。
自社の商品・倉庫にあったロケーション管理を導入しよう
ロケーション管理は、倉庫作業の効率化や精度向上に欠かせない仕組みです。
自社の商品特性や倉庫環境に合わせた管理方法を選ぶことで、作業のスピードアップやコスト削減が期待できます。また、課題を改善するための工夫やシステム導入を取り入れることで、さらに効果的な運用が可能になるでしょう。
自社に最適なロケーション管理を導入し、倉庫業務全体の効率化や顧客満足度の向上に取り組んでください。
倉庫管理システムの記事をもっと読む
-
ご相談・ご質問は下記ボタンのフォームからお問い合わせください。
お問い合わせはこちら