倉庫の棚卸とは?課題や効率化するための方法を紹介
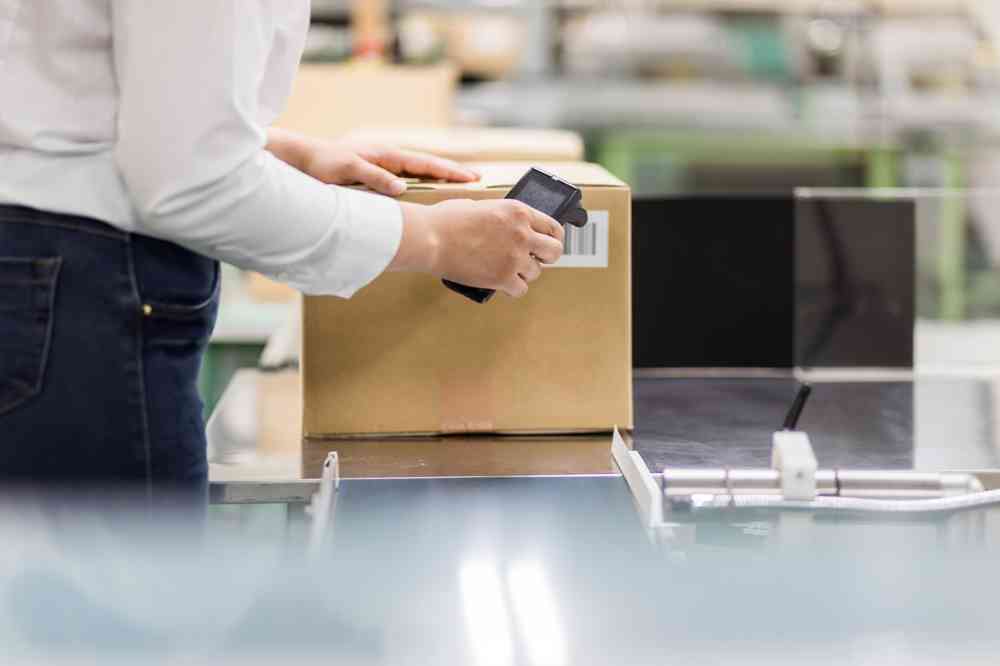
倉庫運営において必要不可欠な棚卸は、倉庫内にある在庫を数える作業です。しかし、在庫数や商品数が多いほど煩雑になりやすくミスも起こりやすいため、効率化やリスク回避のためには対策が必要です。本記事では、倉庫の棚卸をする目的や課題、効率化の方法を解説します。
目次
倉庫の棚卸とは?
倉庫の棚卸とは、倉庫内にある在庫を一つ一つ数え、在庫状況を正確に把握する作業のことを指します。
倉庫で管理している商品は会社資産であり、商品の過不足を把握して管理することは、利益を正しく算出するうえでも非常に重要です。適切な経営判断を行うためにも、倉庫の棚卸しを正確に行いましょう。
棚卸の種類
棚卸は、実地棚卸と帳簿棚卸の2種類に分けられます。それぞれの方法には特徴があり、目的に応じて使い分けられます。詳しく見ていきましょう。
実地棚卸
実地棚卸とは、実際に倉庫内の在庫を目で確認し、手作業で数える方法です。実地棚卸は「一斉棚卸」と「循環棚卸」の2種類に分けられます。
一斉棚卸は、全在庫を一度にカウントする方法です。棚卸以外のすべての作業を止め、担当者全員が在庫を数えるため大掛かりな作業になりやすく、一年の節目にスケジュールを決めて行うことが一般的です。
一方、循環棚卸は、在庫の一部を定期的に少しずつ確認する方法で、ほかの業務を止めることなく進められるのが特徴です。なお、実地棚卸を行う際の具体的な手法としては、タグ方式とリスト方式があります。詳しく見ていきましょう。
タグ方式
タグ方式は、在庫の数を数えた後、「棚札」という伝票に在庫の数量を記入し、棚や商品に貼り付ける方法です。その後、管理者が棚札を回収して集計を行います。
タグ方式は作業に時間がかかるデメリットがありますが、ダブルチェックができるため、確認ミスを減らすことができます。
リスト方式
リスト方式とは、あらかじめ在庫リストを用意し、在庫リストと実際の在庫数を照らし合わせて確認する方法です。
リスト方式は、事前にリストが準備されているため、効率よく作業を進められるメリットがあります。特に在庫数が多い場合は、リスト方式が適しているでしょう。また、リストを使用することで在庫管理の精度も向上します。ただし、リストに誤りがないかを十分注意する必要があります。
帳簿棚卸
帳簿棚卸とは、帳簿のデータを基に、仕入れ数から出荷数を差し引いて在庫数を確認する方法です。帳簿上の在庫を管理するための方法であり、日々の在庫管理に用いられます。
実地棚卸よりも作業負担が少ない点がメリットですが、実際に在庫を数えて確認するわけではなく、あくまでも理論上の在庫数(理論在庫)の把握にとどまります。より正確な在庫管理を行うためには、日々の帳簿棚卸と、定期的な実地棚卸を行う必要があります。
倉庫の棚卸をする目的
倉庫の棚卸には、どのような目的があるのでしょうか。倉庫の棚卸の具体的な目的について詳しく説明します。
利益を正しく把握するため
倉庫の棚卸を行う主な目的の一つは、在庫として残っている商品を正確に把握することにあります。企業がどれだけの在庫を持っているかを知ることは、利益を正しく算出するために不可欠です。
過剰な在庫や欠品がないかを確認することで、売上とコストのバランスを見直し、最終的にどのくらいの利益が得られているかを正確に把握することができます。この情報は、今後の経営判断にも大いに役立つでしょう。
在庫数・品質を正確に把握するため
倉庫の棚卸は、在庫数はもちろん、在庫の中に不良品が含まれていないか、商品の品質をチェックするためにも行われます。
在庫数や品質を把握することは、販売機会損失の防止にもつながります。顧客が商品を購入したいタイミングで良質な商品を提供できるためです。仕入れのタイミングも最適化され、在庫の無駄を最小限に抑えられるでしょう。
在庫管理を改善するため
倉庫の棚卸しをすることで、現在の在庫管理がどれほど適切に行われているかを確認できます。もし問題が発覚した場合には、速やかに原因を明らかにすることで、早期に改善できます。
不適切な在庫管理は、過剰在庫や欠品を引き起こしやすく、コストの増加や販売機会の損失につながります。棚卸を通じて管理体制の見直しを行い、正確な在庫管理を実現することで、企業の競争力を高めることができるでしょう。
倉庫の棚卸の課題
倉庫の棚卸には、いくつかの課題が存在します。効率的な棚卸を行うためには、それらの課題を把握することが大切です。詳しく見ていきましょう。
在庫の数え忘れが発生する
倉庫の棚卸では、在庫の数え忘れがしばしば発生します。特に、棚の奥にしまわれた商品や、別の場所に移動された在庫が見落とされがちです。このような数え忘れがあると、在庫データが正確に反映されず、過剰在庫や欠品といった問題が起こりやすくなります。
倉庫を定期的に整理して商品の数え忘れを防ぎ、正確な在庫管理を維持することが重要です。
在庫の数え間違えが発生する
倉庫の棚卸では、品番が似ている商品やパッケージが似た商品が混在している場合、在庫の数え間違えが発生しやすくなります。特に、似たような品番やラベルを持つ商品が近くに配置されている場合、見間違って誤った数値を記録してしまうことがあります。
このような数え間違えは在庫管理の精度を低下させ、無駄な発注や販売機会の損失につながる可能性があります。正確なラベル付けやチェック体制の強化が求められるでしょう。
記入・入力間違いが発生する
倉庫の棚卸作業では、手書きでの記入やデータの転記、入力時にヒューマンエラーが発生することがあります。特に、大量の在庫を扱う場合、数字の書き間違いや入力ミスが起こりやすく、正確な在庫管理に影響を与えます。
このような間違いが蓄積されると、実際の在庫と帳簿上の在庫に大きなズレが生じ、業務に支障をきたしかねません。ミスを減らすためには、入力のダブルチェックや、倉庫管理システム(WMS)の導入が有効です。
倉庫の棚卸を効率化する方法
倉庫の棚卸を効率的に行うためには、さまざまな工夫が必要です。最後に、具体的な効率化の方法について詳しく説明します。
棚卸マニュアルやルールを作る
棚卸を効率的に行うためには、作業手順を明確にしたマニュアルやルールの整備が重要です。具体的には、在庫の数え方や記入するタイミング、担当者間の役割分担などを定めておくことで、作業がスムーズに進みます。統一されたルールに基づいて作業を進めることで、数え忘れや入力ミスを減らすことが可能です。
また、定期的にマニュアルを見直し、現場の状況に応じて改善することで、さらに効率よく棚卸ができるでしょう。
バーコード・RFID管理を導入する
倉庫の棚卸を効率化する方法の一つとして、バーコードやRFID管理の導入があります。バーコードは在庫を瞬時に読み取ることができ、RFIDは複数の商品を一度にスキャンできるため、手作業の手間を大幅に削減します。数え忘れや入力ミスが減少し、在庫管理の精度が向上するでしょう。
リアルタイムで在庫状況を把握でき、棚卸作業の時間も短縮されます。
倉庫管理システム(WMS)を導入する
倉庫管理システム(WMS)は、倉庫内の在庫や作業を一元管理できるシステムです。WMSを導入すれば、在庫の入出庫状況をリアルタイムで把握できるため、棚卸作業の効率が大幅に向上します。
また、WMSは在庫の配置や数量を自動で追跡する機能が備わっているため、最適かつ正確な在庫管理が実現します。手作業でのミスも減り、業務全体の効率化につながるでしょう。
▷倉庫管理システム(WMS)19選比較|機能や価格・小規模・クラウド向けのシステムを紹介
▷倉庫管理システム(WMS)とは?主な機能や導入メリット・デメリット
自動倉庫を導入する
自動倉庫とは、商品の入出庫や棚卸作業を自動化するシステムを備えた倉庫のことです。自動倉庫を導入することで、作業のスピードが大幅に向上し、ヒューマンエラーが減少します。
また、24時間稼働が可能なため、作業効率も劇的に向上します。特に大量の商品を扱う倉庫では、作業コストの削減や在庫管理の精度向上に大きな効果が期待できるでしょう。
自動倉庫は、労働力不足にも対応できる次世代の倉庫管理方法として注目されています。
専門業者に委託する
倉庫の棚卸作業を専門業者に委託することは、多くのメリットがあります。
まず、専門業者は豊富な経験と専用のツールを持っているため、効率的かつ正確な作業が期待できます。また、棚卸業務にかかる時間や社内リソースを削減できるため、よりコア業務に集中できるでしょう。
特に、大規模な倉庫や複雑な在庫管理を行っている場合、専門業者に委託をすることで棚卸の負担が大きく軽減されます。この点は、専門業者に委託することで得られる大きなメリットです。
作業しやすい環境を整える
倉庫内の整理整頓を徹底することは、棚卸作業の効率を高めるために重要です。商品が整然と配置され、通路が確保されていると作業がスムーズに進みます。
さらに、在庫のラベルや品番が見やすく整備されていることで、数え間違いや確認ミスも減少します。作業しやすい環境を整えることで、従業員の負担も軽減され、全体の作業効率を大幅に向上させることができるでしょう。
自社に最適な方法を検討し倉庫の棚卸作業を改善しよう
倉庫の棚卸作業を効率化するためには、自社の状況に合った方法を選び、改善を進めることが大切です。マニュアルの整備やシステムの導入、環境の整備など、さまざまな対策を検討し実施することで棚卸作業の負担が軽減され、正確な在庫管理が実現します。まずは現状を見直し、自社にとって最適な方法を導入して、業務全体の効率化を図りましょう。
倉庫管理システムの記事をもっと読む
-
ご相談・ご質問は下記ボタンのフォームからお問い合わせください。
お問い合わせはこちら