生産管理の改善事例|主な課題や改善に向けたポイント・手順を詳しく解説
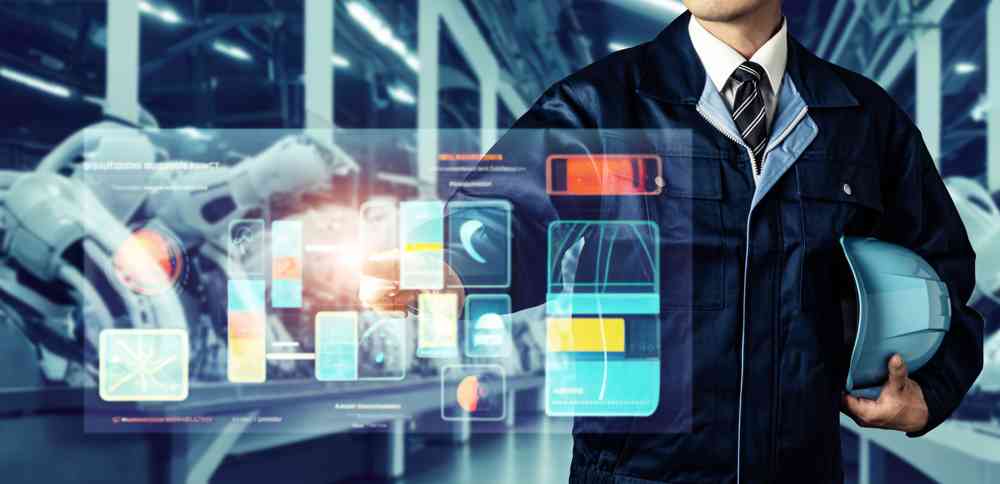
製造業務を「品質」「コスト」「納期」の3つの視点で管理する「生産管理」。企業の市場優位性を確保するために重要な生産管理を適切に行うためには、どうすればよいのでしょうか。本記事では、生産管理の改善事例を紹介し、生産管理の課題や改善に向けたポイントまで詳しく解説します。
目次
生産管理とは?
生産管理とは、生産計画や指示のもとで生産活動を実行・管理することです。具体的には「QCD」と呼ばれる「Quality(品質)」「Cost(コスト)」「Delivery(納期)」の3つの視点から、高い品質の製品をコストを抑えつつ短い納期で納品できるよう管理することを指します。
生産管理に含まれる業務には以下の内容が挙げられます。
- 生産計画の策定
- 受発注管理
- 在庫管理
- 製造管理
- 工程管理
- 進捗管理
- 品質管理
このように、生産管理には複数の業務が含まれ、製品の品質や顧客満足度を高めるためには欠かせません。
▷生産管理とは?目的や工程管理・製造管理との違い、課題を解説
生産管理の主な課題
生産管理の主な課題には以下の5つが挙げられます。
- 納期が遅れる
- 業務が平準化されていない
- 原価管理が難しい
- 人為的ミスが発生する
- 属人化によってノウハウが蓄積されない
それぞれの課題における具体的な原因や影響について、詳しくみていきましょう。
納期が遅れる
生産管理には、納期の遅れがつきものです。資材が予定通り届かなかったり、製造工程がうまく進まなかったりすると、それぞれの業務にトラブルや遅れが生じます。結果、納期そのものに間に合わなくなるのです。
納期が遅れてしまえば、企業の信用低下につながりかねません。全体の納期に間に合っている場合でも、それぞれの業務に遅れが生じると、「納期を早めてほしい」といった変更に対応できないことも考えられます。
業務が平準化されていない
製造現場で生産効率を上げるには、誰がどの業務を行っても同じパフォーマンスを発揮することが大切です。しかし、複数の業務が含まれる生産管理は業務内容が複雑になりがちで、すべての業務を平準化しきれていないケースも多くみられます。
業務が平準化されていない場合、ベテランと新人が同じ業務を行ったとき、品質や生産量に差が生じる可能性があります。業務を行う人によって生産量や品質が変動してしまうと、生産効率が低下するうえ、品質管理が適切でないとして企業の信用低下にもつながりかねません。
▷生産管理における業務フローについて|課題や解決するポイント
原価管理が難しい
製造業では数多くの部品や資材を取り扱うため、すべての原価を正確に管理することは困難です。
しかし、適切な原価管理ができていない場合、何にコストがかかっているかを把握できず、削減できるコストを見落としてしまう可能性があります。また、原価が高騰しても気づきにくいため、販売価格を調整するなどの対応がとれず、企業の利益は減る一方です。
原価管理を行っている企業のなかには、原価を数値として把握しているだけのケースもあります。「その原価が適切なのか」「原価に対して販売価格はそのままでよいのか」といった分析を行っておらず、コスト削減につなげられていません。
原価管理に失敗しているままだと、企業全体の経営にも影響が出る可能性があるため、早急な改善が必要です。
属人化によってノウハウが蓄積されない
業務内容をマニュアル化できていなかったり、判断基準が明確化されていなかったりすると、属人化が起こりやすくなります。スキルやノウハウが蓄積されず、人材育成にも支障をきたすのです。
生産業では製造・営業・仕入れ・運搬など多くの部門が関連し合うため、情報が複雑化しやすく、統一のハードルが高くなります。結果、担当者しか把握していない業務が多くなり、属人化に拍車がかかってしまうのです。
属人化が原因でノウハウが蓄積されないと、担当者が離職した際の引き継ぎが困難になったり、人材育成が難しかったりするなどの問題につながりかねません。人材育成が難しい状態では、適切な人材配置もできない可能性があります。
▷生産管理が属人化する原因とリスク|解消するためのポイントやメリットを解説
人為的ミスが発生する
手作業で行う業務が多いほど、人為的ミスが起こる確率は高くなります。製造業では運搬など、手作業で行わなければならない業務もあるため、人為的ミスを完全になくすことは困難です。
例えば、配送ルートを手書きにした場合、順番や道のりの書き間違いによる配送効率の低下が考えられます。運搬中に製品を壊してしまうケースもあるでしょう。
人為的ミスが発生すると、本来なかったはずのミスへの対応という無駄な時間が生まれてしまいます。防止策として作業員がダブルチェックを行うケースもありますが、人為的ミスは防止できる反面、確認に時間がかかるでしょう。
このように、人為的ミスの防止策や発生した際の対応は、生産性の低下につながりかねません。
▷生産管理の課題とは?解決策やシステムを導入するメリット・おすすめのツールを解説
生産管理の改善事例
生産管理の改善事例を5つ紹介します。実際の企業が行った改善策を参考にすれば、現実感のある対策を講じやすくなるでしょう。
サッポロホールディングス株式会社
サッポロホールディングスでは、生産管理業務のなかでも「ドライバー不足」や「予測・計画業務の属人化」といった物流に関する課題を抱えていました。
そこで同社は、製品をより多く生産するのではなく、物流のキャパシティを考慮した生産・供給補充を計画するという改善を図ったのです。同時に、需要予測や計画業務にシステムを導入し、業務の自動化を図りました。
このような改善策により、生産と物流の均衡をとることに成功しています。製品の過不足や車両が足りていない問題が改善されたほか、属人化の解消効果も得られています。
[参照元:サッポロホールディングス株式会社「サッポログループがAI技術を活用したロジスティクス領域の計画主導型システム導入」]
株式会社東京ダイヤモンド工具製作所
東京ダイヤモンド工具製作所では、システムの老朽化が進んだことで、業務に対してシステムが機能していないという課題を抱えていました。それにくわえて、業務によってシステムを分けていたため、データの二重入力が生じるという課題もあったのです。
そこで同社はシステムを一新し、生産・原価・販売・会計の全システムを連携させ、あらゆるデータを一元管理できるよう改善を行いました。
この改善により、データを複数のシステムに入力する手間が削減されたうえ、データの見える化も促進しています。情報伝達の遅延やミスの減少・原価管理にかかる時間の短縮・データの2次活用といったメリットにもつながりました。
[参照元:キャノンITソリューションズ株式会社「販売/生産/原価/会計が連携した基幹システムの導入」]
株式会社山口技研
Excelでの生産管理に限界を感じていた山口技研は、生産管理システムの導入に踏み切っています。ファイルやシート間の連携が複雑化し、操作ミスでデータを消失するなど、Excelにありがちな課題が山積していました。
システムには帳票作成機能を搭載した製品を選択し、機能の活用によって収益率を10%向上しています。
また、製造工程や仕入の進捗状況をシステムから簡単に確認できるようになったことで、月あたり100時間の工数削減も達成しました。ほかにも、図面をデータ化したことで検索性が向上し、知的財産として活用しやすくなったなどの効果も得られています。
[参照元:株式会社テクノア「『TECHS-BK』で業務効率化、 社員の意識向上を実現」]
株式会社三信精機
三信精機は、生産管理における情報の属人化や、事務業務の人為的ミスが多いなどの課題を抱えていました。その主な原因となっていたExcel管理を改め、生産管理システムを導入したのです。
システムを選んだ決め手は、自社の業務に合致している機能が網羅されていることでした。導入後すぐに、業務における人為的ミスの減少や事務の工数削減の効果を感じたといいます。事務業務は月あたり約63時間もの工数削減が実現しました。
システム上で生産管理に関するあらゆる情報を一元管理できるようになったため、情報の属人化が解消しています。各部門で情報の有効活用が促されるなどの意識改革にもつながり、粗利率が2倍になる嬉しい結果を得られました。
[参照元:株式会社テクノア「データの“見える化”で社員の意識が劇的に変化」]
枚岡合金工具株式会社
枚岡合金工具が行ったのは、機械の稼働状況を監視するカメラシステムの導入です。きっかけは、機械の稼働を可視化して生産性アップを目指そう、との意見が社員から挙がったことでした。
稼働状況を監視するカメラシステムは、人や機械の動きを検知することで、機械が稼働しているかどうかを把握できるというものです。曖昧だった停止時間の把握と有効活用を狙い、より多くの製品を生産する目的から導入が進みました。
カメラシステムの導入により、機械の稼働状況を把握できるようになっただけでなく、全社員が機械の稼働率を意識して取り組むようになりました。その結果、生産効率はシステム導入前の1.7倍にまで伸びています。
[参照元:株式会社テクノア「機械稼働率の「見える化」で社員の意識が変化 生産性向上を実現!」]
生産管理の改善に向けた手順
生産管理の改善に向けた手順は以下の通りです。
- 業務を可視化する
- 業務課題を洗い出す
- 改善計画を策定し実行する
- 評価と改善を繰り返す
業務が広範囲に及ぶ生産管理において効率的な改善を目指すために、それぞれの手順を把握しておきましょう。
業務を可視化する
担当者だけでなく誰もが業務内容を把握できるよう、業務を可視化しましょう。業務が可視化されていない状態では課題を発見しにくくなり、「何を改善したらよいのか」「そもそも改善の必要性を感じない」などの状況に陥り、改善に向けたアクションを起こせません。
そのため、業務工程をフローチャートに書き出したり、業務担当者に直接ヒアリングを行ったりして、業務を可視化させましょう。生産管理に関わる業務は部門をまたぐものも多いため、異部門の担当者が必要な情報を確認できるよう可視化することが大切です。
業務課題を洗い出す
業務を可視化できたら、生産管理にどのような課題があるかを洗い出しましょう。「在庫の数を把握しにくい」「部品の管理場所が製造現場から離れている」といった現場の意見も、課題と受け止めることが重要です。これらは、業務を非効率にしていたり、負担を増やしていたりする原因ともとれます。
なお、意見などをもとに洗い出した業務課題には、優先順位をつけていきましょう。同時に、改善策の実行が後回しにならないように、それぞれの課題をいつまでに改善するのかという期限も決めることが大切です。
改善計画を策定し実行する
課題に対して具体的にどのような改善策を実行するのかを計画します。1つの課題に対して複数の改善策を検討することが大切です。
生産管理の改善策によって、メリット・デメリットは異なります。例えば、即効性の高い改善策であっても膨大なコストを要するもの、コストが少なくすぐに実行できても効果が出るまでに時間がかかるものなど、内容によりさまざまです。
そのため、洗い出した課題に対して複数の改善策を検討し、自社にとってどの方法が最適かを見極めたうえで計画を策定しましょう。担当者の選任も行い、計画に沿って改善策を実行していきます。
評価と改善を繰り返す
改善計画を実行したら、「改善の効果は出ているのか」「新たな課題はないか」など、改善計画の評価を行いましょう。
改善を目的としたにもかかわらず、かえって非効率になったなど、改善計画の実行によって状況が悪化するケースも少なくありません。作業の迅速化を狙って部品の保管場所を変えたものの、実際は取りにくさが目立ったなどの例が挙げられます。
生産管理の現状を正確に把握するためにも、改善計画は実行するだけではなく、評価と改善を繰り返すことが大切です。
生産管理の改善に向けたポイント
生産管理の改善に向けたポイントを6つ紹介します。改善策に取り組む際に意識すれば、より効果的な改革を実行できるはずです。
「無くす」「減らす」「変える」3つの視点で考える
生産管理に限らず、業務改善を行う際は「無くす」「減らす」「変える」の3つの視点で考えることが大切です。具体的には、無くしても問題ない業務が慣習的に残っていないか、処理の回数や量を減らすことはできないかなどを検討します。
基本は「無くす」「減らす」「変える」の順で業務改善を検討するほか、従業員への負担やコストとのバランスを考慮して優先順位を決めましょう。生産管理の改善には幅広い業務に目を向けなくてはならず、複数を同時に実行するのは現実的ではないため、的確な順位づけが重要です。
業務を定型化し属人化を防止する
製造業における生産管理業務では、業務内容が複雑なうえ、現場ごとに担当者が存在するため、属人化が起こりやすい傾向にあります。
業務が属人化している状態だと、担当者不在時の対応ができなかったり、引き継ぎが困難になったりするなどの弊害が生じます。また、新人教育にも支障をきたすため、マニュアルの整備を行うなどして業務の定型化を進めなくてはなりません。
属人化を防ぐには、業務を定型化することが大切で、特定の個人にだけ作業負担が偏ることが減り、属人化を予防可能です。また、マニュアルによって全員が同じ方法で業務を実行できれば、品質の維持や生産性の向上も期待できます。
スモールスタートで改善に取り組む
生産管理は製造業において中枢を担う業務であるため、改善施策は広範囲に影響を及ぼします。はじめから大規模に取り組んでも、改善に伴う業務負担の増加や現場の混乱を招く恐れがあるので、スモールスタートを意識することが大切です。
まずは小規模で改善に取り組み、効果が感じられれば、徐々に改善する業務範囲を広げていきましょう。各部門からはじめていき、順に部門間の取り組みを進めるなど、異なる業務担当者が円滑に連携できるような工夫も盛り込んでください。
スモールスタートで改善の成功を繰り返すうちに取り組みのコツをつかめば、大きな改善策に活かすことができます。
PDCAサイクルを意識する
PDCAサイクルとは、「Plan(計画)」「Do(実行)」「Check(評価)」「Action(改善)」の4つのプロセスを繰り返すフレームワークのことです。生産管理の改善においても不可欠な考え方となります。
業務改善をたった1度行っただけで、すべての課題が解消されることはほとんどありません。計画の実行以外にも、評価や改善といったPDCAサイクルを意識しながら継続することで、効果的な改善効果が望めるのです。
1つの課題が解消されても、また新たな課題が見つかるはずです。1度の取り組みで満足せず、PDCAサイクルを回しながら、生産管理の改善を安定して行えるようにしましょう。
▷PDCAとは?サイクルを回す意味や具体例・失敗する原因をわかりやすく解説
現場の声に耳を傾ける
業務改善を行う際は、現場の意見を取り入れるようにしましょう。どのような改善策に取り組むかは、最終的に経営層が判断します。しかし、経営層は現場の状況や業務内容を詳細まで把握できていないことも多く、改善策と現場の希望とが異なる場合があります。
そのため、改善策を検討する際は、必ず現場の従業員にヒアリングなどを行うべきです。より現実的で効果的な改善策の立案につながるほか、自分の意見が採用されることで従業員のモチベーションアップも期待できます。
生産管理システムを活用する
生産管理に関するあらゆるデータを一元管理するシステムを導入すれば、多くの業務を改善可能です。生産計画の策定・在庫管理・工程管理・進捗管理など、さまざまな業務を一か所で管理できます。
Excelや紙による管理を生産管理システムに変えるだけで、人的ミスや工数を大幅に削減し、業務の効率化が図れます。データによって業務内容の可視化が進むと、課題の究明もしやすくなるでしょう。
なお、生産管理システムの導入を成功させるには、自社の求める機能やコストとのバランスを考慮することがポイントです。従業員に対する事前の説明や操作方法の研修を実施するなど、十分な準備を行いましょう。
▷【2024年最新】生産管理システム18選比較!選び方や活用方法・主な機能を紹介
改善事例を参考にして自社の生産管理を見直そう
生産管理は業務内容が複雑なため、課題を抱えている企業は少なくありません。しかし、自社の課題を見極め、最適な改善策を実行すれば、業務効率や生産性を向上させることが可能です。
実際に、業務の進め方を変更したりシステムを導入したりしたことで、課題を解消した企業事例がいくつもあります。今回紹介した改善事例を参考にしながら、自社の生産管理業務を見直していきましょう。
生産管理システムの記事をもっと読む
-
ご相談・ご質問は下記ボタンのフォームからお問い合わせください。
お問い合わせはこちら